The following guidelines are designed to describe the process of a typical ITAC energy assessment center in the performance, creation and delivery of the primary products of the ITAC program; the industrial assessment and the industrial assessment report.
Scope of Industrial Assessments
- The Industrial Assessment Center (ITAC) is an energy center based in the engineering department of a major University, and supported by the Industrial Technologies Program at the US Department of Energy.
- The ITAC team is comprised of one (or more) professors, and engineering students. One of these students is designated the report lead and another the safety lead.
- The typical ITAC industrial assessment is expected to be conducted in one day.
- The resultant Assessment Report is designed to help medium sized manufacturers identify ways to save energy, reduce waste, and improve productivity while providing engineering students with hands-on training in manufacturing plants.
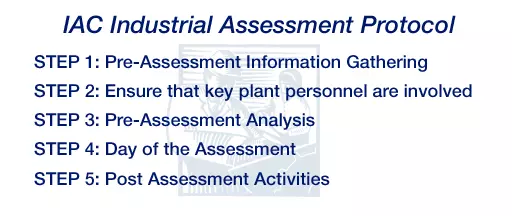
STEP 1: Pre-Assessment Information Gathering
Client is sent a Pre-assessment Form. This form includes:
- Size of Plant and plant layout
- Industry type (SIC/ NAICS code) and process description
- Production levels, units and dollars, operating hours
- A one year history of utility bills
- List of major energy consuming equipment
STEP 2: Ensure that key plant personnel are involved
- Plant manger
- Energy manager
- Environmental personnel
- Maintenance personnel
STEP 3: Pre-Assessment Analysis
- Analyze the manufacturing process
- Chart and graph utility bills
- Analyze utility bills for trends and errors; establish unit cost of energy
- Start Plant profile using QuickPEP
- Identify key energy systems
- Review design and other technical documentations
- Identify possible energy saving potential recommendations using ITAC database
- Develop Assessment Day Strategy
STEP 4: Day of the Assessment
- Introduction
- History of the ITAC program, ITP and BestPractices
- Distribute BP tools, case studies, tip sheets
- Description of manufacturing process and operations
- Is this a typical day?
- Run through process following material flow
- Discussion of inventory levels
- Questions about defects, bottle necks and waste materials
- Present charts and tables of utility bills
- Plant Tour
- Conduct in direction of the material flow
- Plant Manager to conduct tour
- Only one person will ask questions
- Conceptual tour, no data taken
- Meeting room debriefing
- Discuss process, ask questions
- Develop and plan for the afternoon
- Create specific tasks and divide into teams
- Review notes and brainstorm (Lunch)
- Develop list of potential energy saving opportunities
- Ensure that everyone has clarity of process and potential recommendations
- Refine List of opportunities to be investigated
- Decide what information needs to be gathered, measured, monitored
- Assign teams to specific tasks
- Make plans to meet at assigned time and place
- Data Gathering - Conduct Measurements, monitoring and diagnostic testing
- Motor systems
- Heat processes
- Cooling processes
- Water Use and pumps
- Ventilation
- Compressed Air
- Building Systems
- Delivery and distribution systems
- Exit Interview
- Discuss findings with management
- Prelimiary estimate of potential savings
- Prioritize recommendations of analysis
STEP 5: Post Assessment Activities
- Conduct engineering and financial analysis
- Develop first order estimates of implementation cost
- Deliver report to client, upload date to ITAC database
- Contents of an ITAC Report
- Executive Summary including summary of Recommendations
- Plant Description
- Process Description
- Resource Charts and Tables
- Major Energy Consuming Equipment
- Best Practices
- Description of Individual Energy Saving Recommendations
- Follow-up to Report
- Call client two week to ensure delivery and answer questions
- Call client in 6-9 months for implementation data
- Upload data to ITAC database
- Inquire about potential for Case Study of project(s)